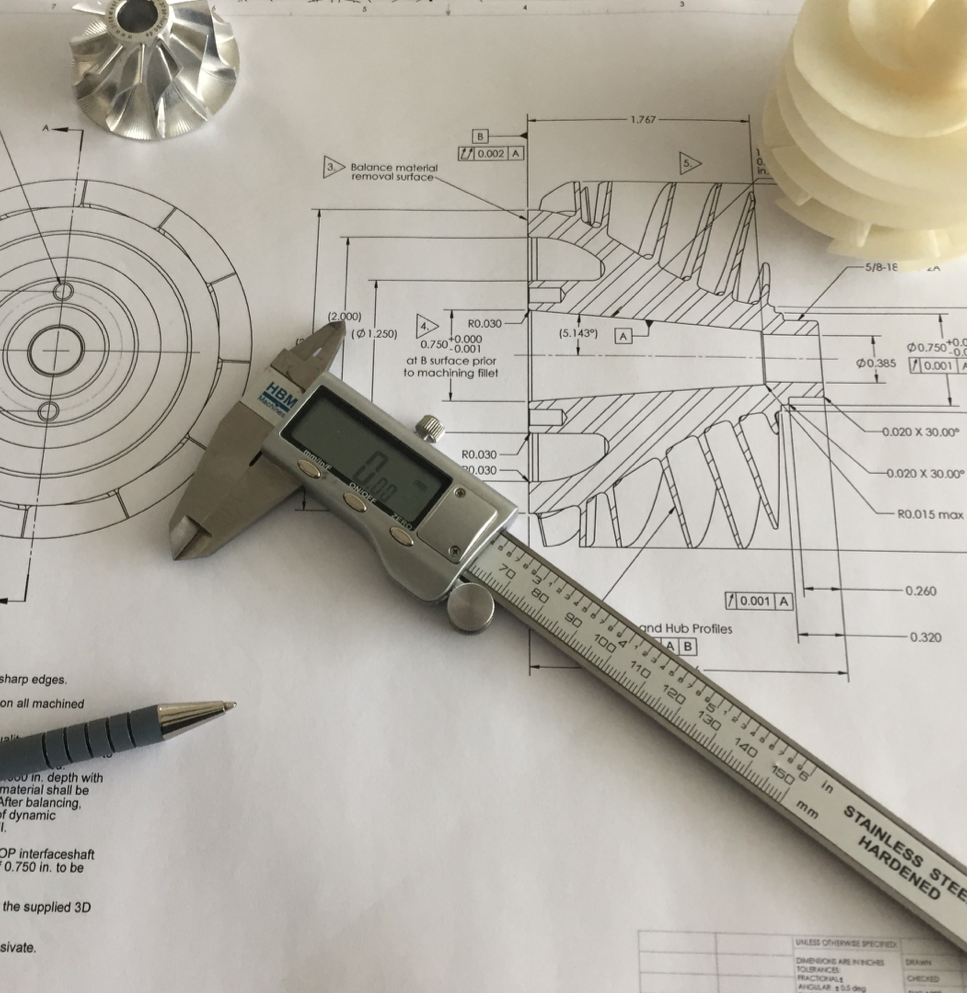
Design Optimization of Splitter Blades for Rocket Engine Turbopumps
​
Student: Francesco Torre
Co-authors: Dr. M. Pini, Prof. Y. Kawata
​
In this project we present and validate a shape optimization framework for the design of splitter blades that extends the operative range under cavitation while maintaining the wetted performance of rocket engine turbopumps. For a target turbopump application, the optimization framework allows for independent changes to the blade angle distributions across the span and to the pitchwise position of the splitter blades while preserving the thickness distributions.
The optimization is conducted with a surrogate-based gradient method. The geometry is optimized at a fixed cavitation number corresponding to a 5% head coefficient drop-off, while constraints are imposed on the wet pump performance. It is found that this approach, coupled with the surrogate-based optimization process, reduces the computational cost of the optimization process by minimizing the number of multiphase calculations.
The numerical results suggest that the optimized splitter blades successfully increase the pump operative range by 2.2% and increase the head coefficient by 5.3% compared to the baseline case with non-optimized splitters. These results are corroborated by experiments conducted in a closed-loop water test facility. Several pump geometries are tested through rapid prototyping using additive manufacturing. The experimental data validate the optimization framework, demonstrating a 4.7% increase of pump operative range and a 7.6% increase in head coefficient. The calculations are used to gain insight in the physical mechanisms for the performance improvement. The analysis of the results indicates that the improved performance is due to the optimized position and shape of the splitter blades which increase the pump slip factor. The paper breaks new ground in defining an efficient design methodology for the improvement of cavitating performance in rocket turbopumps.